Với sứ mệnh tăng tốc chuyển đổi số doanh nghiệp, NSV mang tới những giải pháp hỗ trợ mọi công đoạn trong phát triển sản phẩm từ thiết kế, mô phỏng, gia công cho tới quản lý vòng đời sản phẩm. Sau 20 năm hoạt động, chúng tôi tự tin có thể mang tới cho quý khách những giải pháp tốt nhất được cá nhân hóa cho từng doanh nghiệp giúp quá trình số hóa trở nên dễ dàng hơn.
Đọc thêm

Dịch vụ tiêu chuẩn Nhật Bản
Là thành viên của tập đoàn ARGO GRAPHIC, NSV cam kết mang đến cho bạn trải nghiệm dịch vụ khách hàng tốt nhất theo tiêu chuẩn Nhật Bản.
Đối tác Vàng của Dassault Systèmes
Là Đối tác Vàng duy nhất của DS tại Việt Nam, chúng tôi cam kết mang đến sản phẩm và dịch vụ tốt nhất cho khách hàng.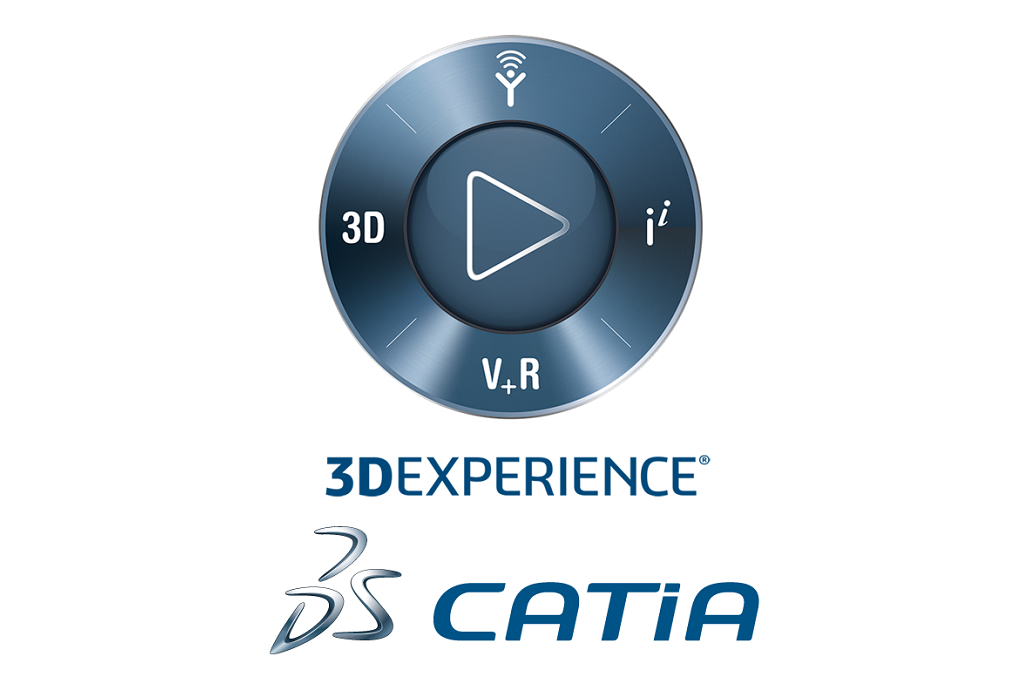
Phần mềm CATIA 3DEXPERIENCE
Với việc là đối tác hạng Vàng của Dassault Systèmes, chúng tôi tự hào là nhà phân phối độc quyền phần mềm CATIA 3DEXPERIENCE tại Việt Nam.
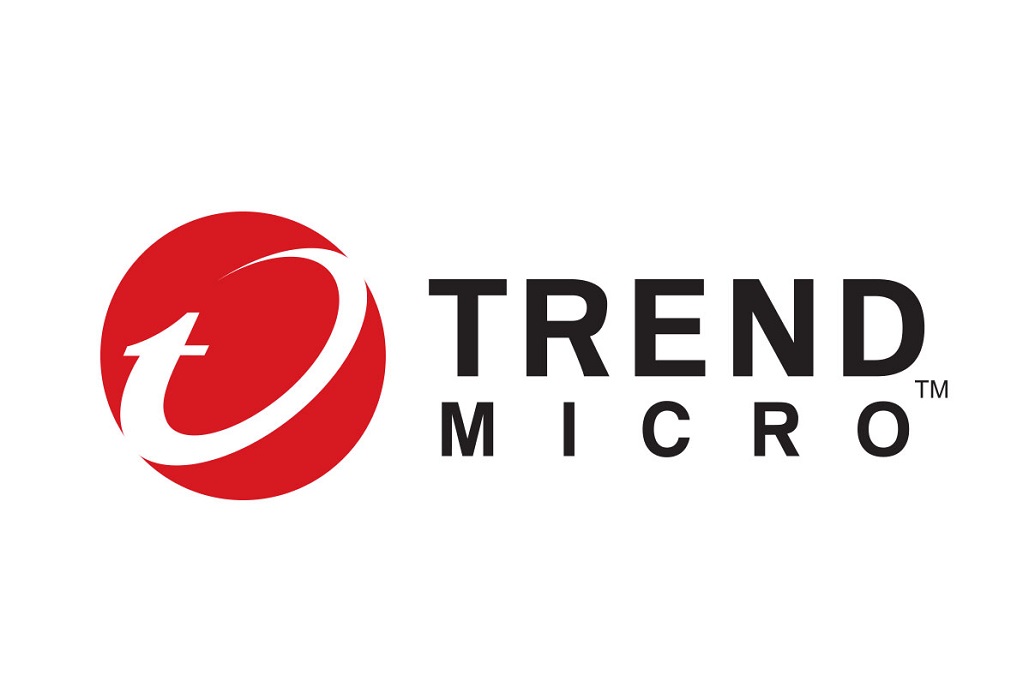
Giải pháp bảo mật của Trend Micro
Là đối tác của Trend Micro, hãng phần mềm Cyber Security hàng đầu của Nhật Bản, NSV cung cấp giải pháp tư vấn và xây dựng hệ thống An Ninh Mạng giúp nâng cao bảo mật trọng vận hành của khách hàng.
ĐỐI TÁC CỦA CHÚNG TÔI
Các đối tác luôn đồng hành cùng NSV trên hành trình mang tới giải pháp bền vững cho doanh nghiệp
KHÁCH HÀNG
Các khách hàng đã và đang đồng hành cùng NSV trong suốt 20 năm qua.